One can feel the morning chill amid the shining Sun as Sanjana, along with a bunch of other young boys and girls, deboards the bus.
Pacing towards the entry gate to punch in, she rushes to her designated workspace at the state-of-the-art shop floor of a locomotive company.
Sanjana is the first girl from her locality to step out of the house and join the workforce in this modern factory.
“I learned to speak in English and acquired technical knowledge after working in the factory,” says a confident Sanajana.
There are many like her, including Gudiya, Rohit, Priti, and Bipin, who have joined duty in the first shift at the sprawling electric locomotive factory situated in a remote township of Bihar.
Welcome to the Madhepura Electric Locomotive Private Limited (MELPL) — built under a public-private partnership between the Indian Railways and the French major Alstom in northeast Bihar.
In line with the Government of India’s ‘Make in India’ initiative, Alstom is manufacturing about 12,000-horsepower (HP) locos in Madhepura for heavy hauling purposes.
They have rolled out as many as 360 high-horsepower locos until September-end this year.
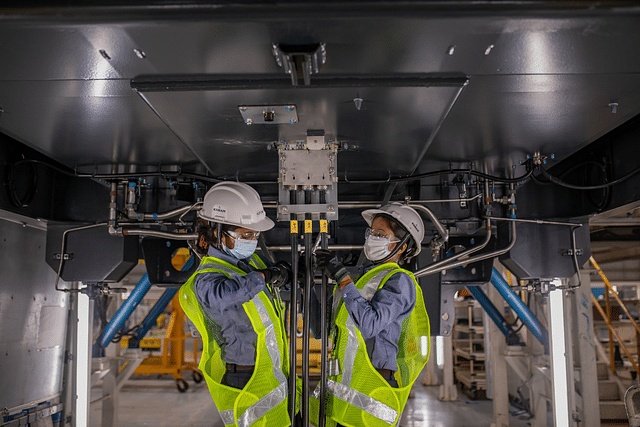
Gudiya, who works at the Madhepura loco facility, says, “I was a bit nervous in the beginning as I had never seen a factory before.”
She is from a nearby village and works as an associate.
Sanjana was initially nervous, too. “I was scared at the beginning, but I managed it with the support of the staff and my parents,” she said.
She is from the nearby Ganeshasthan village. She joined the loco factory as an apprentice three years ago.
The most modern loco factory in Bihar is also the largest foreign direct investment in the railways sector, and has a strategic role in creating a multiplier effect on the economy.
According to the locals, a market complex has come up at Madhepura after the factory began operations. There was no proper market here earlier, and people had to go to Patna for everything.
The Madhepura facility brings together the strength of both the Indian Railways and Alstom.
One can feel the buzz inside the factory — safety, punctuality, and timely delivery, which are keywords for the skilled staff, and regular efforts to up the technology are palpable.
The MELPL is a joint venture between the French major and the Indian Railways, each holding an equity share of 74 per cent and 26 per cent, respectively.
“We consider our manufacturing site at Madhepura as one of the strongest endorsements of ‘Make in India’. By manufacturing these powerful e-locos domestically, we have become the sixth country in the world to produce high-horsepower locomotives indigenously,” said Anil Saini, Managing Director (Rolling Stock & Components), Alstom India.
There are about nine to 10 locos being manufactured in a month at the factory. The target is 100 locos in a year.
Spreading over 326 acres of land, the modern loco factory occupies 120 acres and the staff colony, 90 acres.
Most of the land has been acquired from seven nearby villages, including Sripur, Chakla, Ganesh Asthan, and Tuniyahi.
“We are actively investing in uplifting the community across seven villages in and around Madhepura, covering education, healthcare, women empowerment, and skilling to support the local communities,” Saini said, adding, “Through our initiatives in the region, we have touched the lives of more than 25,000 people.”
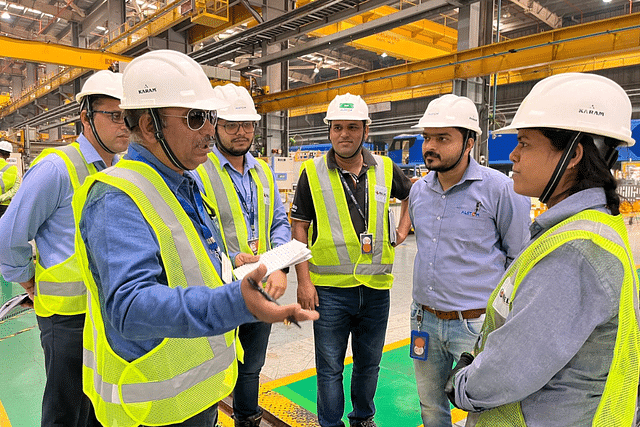
The factory is expected to manufacture and deliver a total of 800 electric locos to the Railways until 2028.
Bipin Kumar, who is from a nearby village and working at the factory since its inception, said, “I would like to continue in the factory to witness the rolling out of the 800th locomotive from Madhepura factory.”
Sanjeev Gupta, whose maternal uncle was in the Railways, is involved in balancing bogey and load-testing machines as an engineer in the company.
“The train engine has always fascinated me, and I wanted to be part of the loco manufacturing team. With the setting up of this factory in the area, my wish has been fulfilled,” Gupta said.
For Priti, who is a logistics operations officer, her parents were against the idea of her joining the company. Priti’s parents were then counselled by senior Alstom employees to allow her to join work.
“For me, a dream comes true,” said an excited Priti.
“I used to see bright lights at the factory from our village and was dreaming of working there someday. Now, I am here,” a visibly beaming Priti said.
While the company has engaged skilled employees for the manufacturing of electric locos, recruitment for the canteen, housekeeping, and electrical works, among others, is done within the region only.
Since the Indian Railways is marching towards 100 per cent electrification and sustainable mobility, the new locomotives will not only bring down operating costs for the Railways, but will significantly cut down greenhouse gas emissions, as well.
The multi-colour production dashboard at the factory is crucial for monitoring output. Placed prominently at a vantage point, one can see three colours — red, yellow, and green.
Updated on an hourly basis, the different colours indicate the stage of manufacturing of the locos.
A staff member tells me “it is dynamic” and provides “specific positions on a real-time basis.”
Using the latest technology, it is a seamless operation from the zero point, representing the start of work, through to the end result of delivery to the Railways, which is the customer.
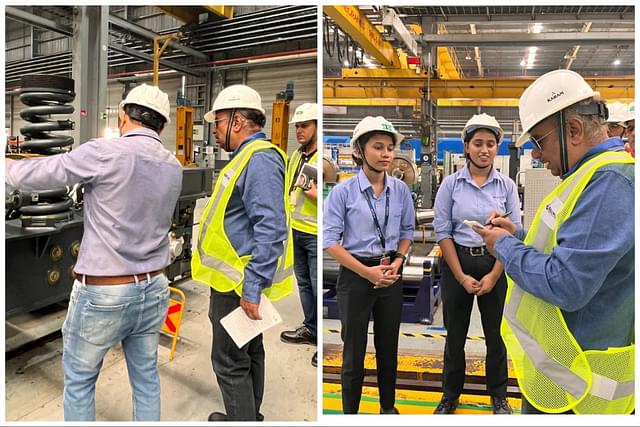
The manufacturing facility and the large investment made in this remote township is also helping in the socio-economic development of the region.
“We have localised our supplier base, which is a significant step towards building local engineering capabilities,” Saini said.
“We have progressively achieved over 90 per cent indigenisation and that has created more than 10,000 direct and indirect jobs in Bihar, Uttar Pradesh, and Maharashtra.
“The e-loco project has transformed Madhepura into a home to India’s most powerful e-loco manufacturing unit.”
As per the 2011 census, 95.58 per cent of the population of Madhepura district lives in the rural areas of villages.
According to the Railways, for the Dedicated Freight Corridor (DFC), it is an optimised locomotive. The 12,000-HP locos are successfully hauling freight on the Eastern DFC and its feeder routes. The advantage is that it can take one extra wagon also.
The Railways maintains that the factory has contributed significant goods and service tax (GST) to the state exchequer.
As an oasis in the midst of a vast tract of land, the Madhepura factory is a success story for many, as one can tell that life is what you make of it.