Setting a benchmark for loco maintenance, the depot has a war room — a crucial tool for speedy maintenance of locomotives.
Currently managed by Alstom, the Nagpur depot would be handed over to the Railways in 2026 after providing maintenance service to 250 locos.
Aiming at making high powered locomotives available to the Indian Railways, for its heavy haul operation for maximum amount of time after maintenance, Nagpur depot manufactured by Alstom has provided service to 42 locos till date.
Equipped with state-of-the-art-machineries, integrated warehouse and a war room among others, the modern maintenance depot at Nagpur — with 26 percent Railways stake and a built capacity of 250 locos — is part of the Make-in-India initiative of Indian Railways.
In order to cater to the heavy haul operation particularly in the Dedicated Freight Corridor (DFC), Alstom is manufacturing 12,000 horsepower (HP) electric locomotives at Madhepura in Bihar.
After rolling out from Madhepura, the locos come to the depot for scheduled maintenance. Till now 42 locos are being serviced here, said Uttam Rajan, Site Managing Director of the depot.
Like Quick Response Team (QRT), the depot has a Prompt Response Team (PRT) composed of trained personnel equipped with tools and critical spares.
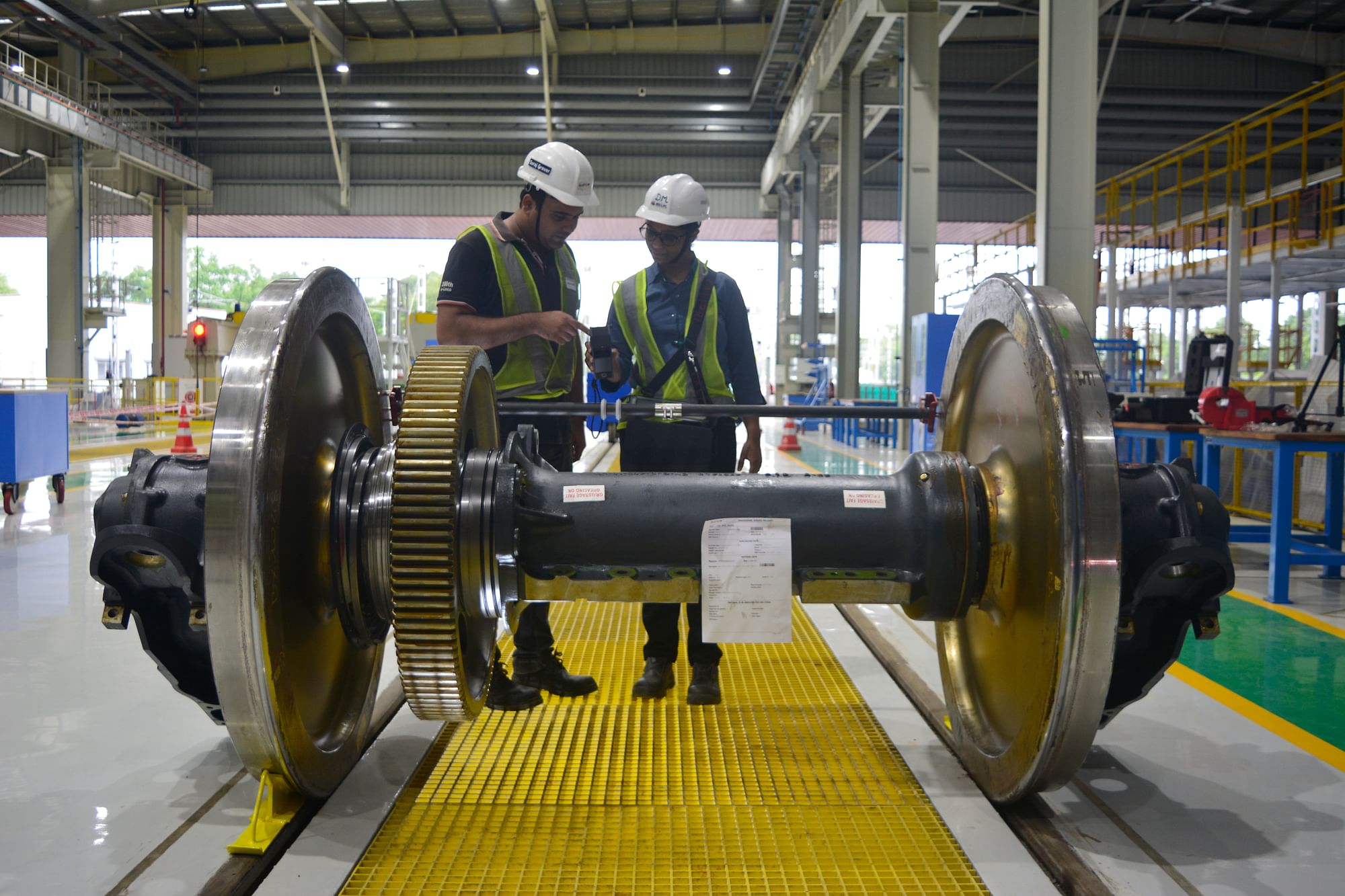
At times we send our PRT directly to the mainline to attend to the fault so that time can be saved from coming to the depot, Rajan added.
Following a modern concept and setting a benchmark for loco maintenance, the depot has a war room — a crucial tool for speedy maintenance of locomotives.
All locos are equipped with IOT-based train-to-ground communication systems, which provide real time information on critical parameters to determine the health of locos in the field round the clock.
Entire route is geo-tagged, which allows the team in the war room to determine the location, speed, kilometres run and other operational data for locos operating across India.
“At the depot everything moves at a faster speed as we have PRT to address the issue related to loco functioning without delay. The idea is to make available locos to the Railways with minimum loss of time,” Rajan said.
Situated at a 16 acre of land, work for the Rs 150 crore depot was started in 2020 and immediately after, the pandemic struck.
However, despite Covid, work continued amid the global chip crisis and got completed in May 2022 and it was dedicated to the nation in December 2022.
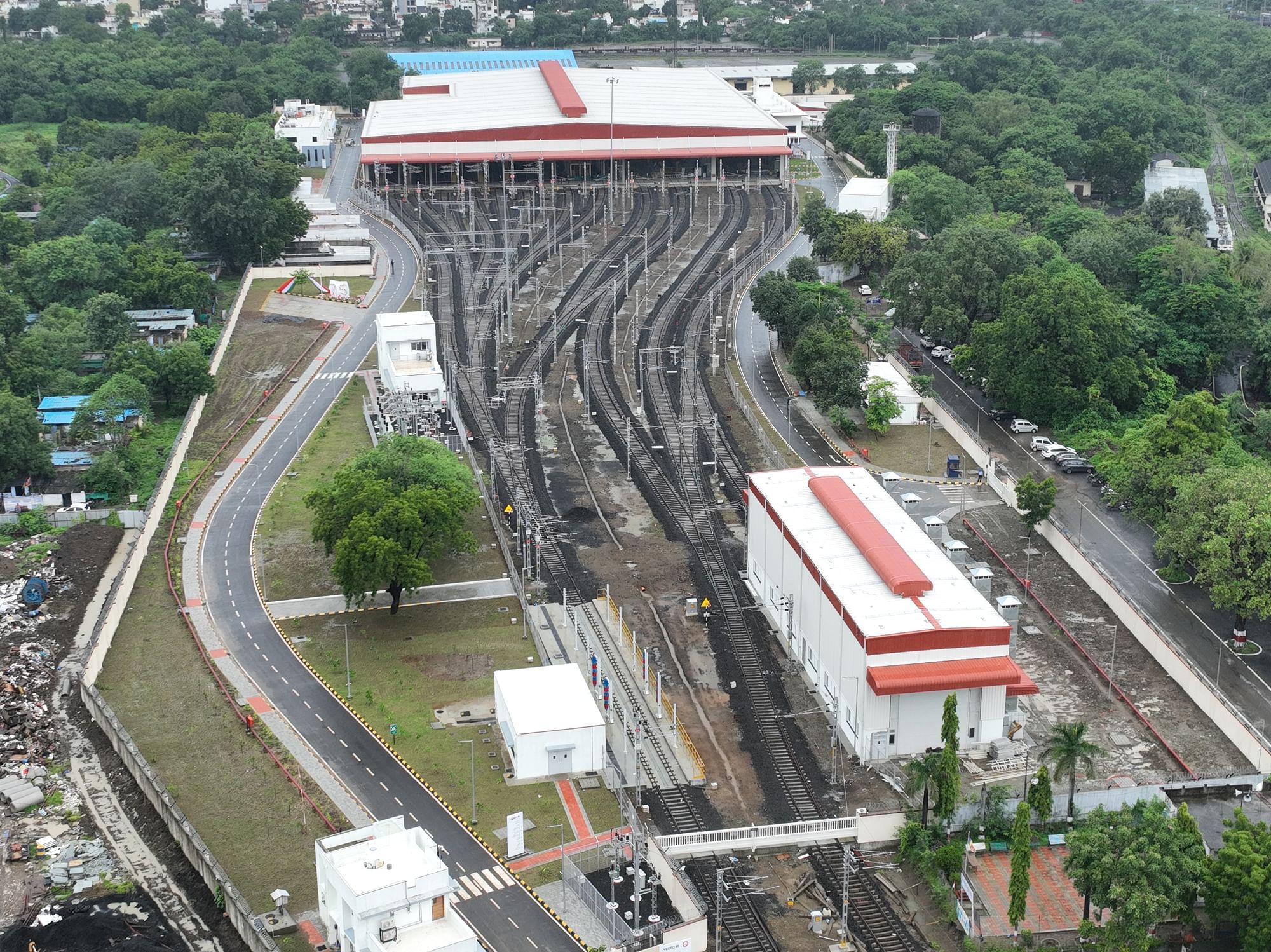
The first loco came for maintenance in September 2022 and till date 42 locos have been maintained at the facility. These locos have run over 1.1 million km across the country without glitches.
With the help of new technology, the depot also has a fully automated loco wash plant.
“If the washing and cleaning of loco is carried out manually it would take half a day, but in the wash plant it takes just 37 minutes,” said Rajan.
Besides overhead crane and bogie drop system, and platform for roof access, the depot has an integrated modern warehouse which has 3,000 unique parts.
The warehouse is temperature controlled, with fireproof cabinets, and a humidity chamber which stores parts in controlled temperature.
In order to achieve high operational efficiency, the depot has a kitting area which prepares materials for loco maintenance even before the loco arrives at the shed — to have quick turnaround time.
The shop floor of the depot provides advanced logistic solutions which ensures availability of materials all the time with minimum human intervention.
Stressing on the working model of the depot, the director said, “We try to develop a working culture established on a foundation of continuous improvement through APSYS (Alstom Performance System). Our work culture is based on AIR (agile, inclusivity and responsibility).”
The depot is ergonomically designed for crew comfort fitted with a high volume low speed fan.
Following the zero discharge method, all liquid outflow is being treated at ETP and STP as the depot has special focus on environment and sustainability.
Gardening and washing are maintained through recycled water. The depot is also equipped with a rain water harvesting system to recharge the groundwater level.
Currently managed by Alstom, the Nagpur depot would be handed over to the Railways in 2026 after providing maintenance service to 250 locos.
The Madhepura factory is producing eight locos in a month at present.